Tongji University received a letter of thanks from Commercial Aircraft Corporation of China Ltd. (COMAC) not long ago. The letter said that on September 29 this year, the domestically developed C919 large passenger jet had undergone all the test flights and obtained an airworthiness certificate from the Civil Aviation Administration of China. Sincere gratitude was given to Tongji University for its strong support and assistance in scientific and technological innovation of large aircraft, cooperation with the industry in teaching and research, and for its important contributions to promoting the development of the C919 large passenger jet and obtaining the certificate.
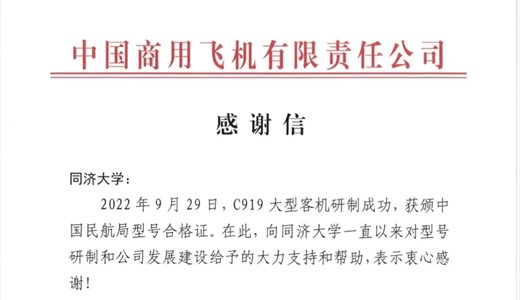
Tongji University received a letter of thanks from the Commercial Aircraft Corporation of China.
Research teams from the School of Aerospace Engineering and Applied Mechanics, the School of Physical Science and Engineering, and the School of Mechanical Engineering participated in the development of the C919 large passenger jet and cooperation with the industry in talent cultivation, contributing to the "Tongji Power" for the development of China's large aircraft cause.
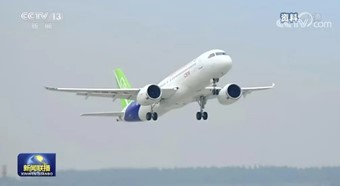

Tongji University participated in the development of C919 large passenger jet.
School of Aerospace Engineering and Applied Mechanics
Professor YUAN Guoqing, director of the Institute of Composite Materials and Structures, School of Aerospace Engineering and Applied Mechanics, participated in the work of composite structures for civil aircraft. As early as the ARJ21 development stage, the state initiated a project to research the full-size composite tail and control the surface of civil aircraft. Since then, Professor YUAN has embarked on his research journey on aircraft composite structures and has undertaken two research projects. The results of his numerical analysis and test analysis have provided strong technical support for the detailed design of composite tail structures.
During the C919 development, Professor YUAN also undertook two research projects. One of them was the type selection test research of C919 composite wing panel profile parameters, and the other one was the type selection test research of C919 aircraft tail composite sandwich structure connection.
Professor GAO Yukui of the same School served as the deputy chief designer of the C919 passenger jet during his tenure in COMAC. He was responsible for researching the strength, shot peening process, and fatigue performance of the aircraft body. He became a member of the C919 aircraft static test team and a member of the C919 aircraft static test commando. He participated in the launch of the first flight of the C919 aircraft in 2017 and the 2.5g dynamic balance condition energy test (limited load) of the whole aircraft. He checked the shot peening process and conducted the on-site quality inspection. He also traveled to different organizations in China to check the effectiveness of certain processes and the reliability of the experimental data, providing technical support for the closed loop of some key issues before the first flight of the aircraft. In particular, through close cooperation with people from the fatigue strength room, he worked out the quantitative impact of the body shot peening process on fatigue performance, and finally passed the audit of the Civil Aviation Airworthiness Bureau, making contributions to the delivery of the first aircraft.
Professor ZHU Yanjuan of the same school participated in the parametric design of the overall geometric body shape of the large passenger jet. Parametric geometric shape design with dimension-driven constraints is one of the main features of the C919 geometric shape design, which was recognized and accepted by international aircraft design and manufacturing experts. She is a member of the joint engineering team of China's large passenger aircraft.
In terms of composite molding technology for large aircraft components, Professor LIU Ling from the same School analyzed microstructure and resin matrix flow evolution during the molding process of a new composite intermediate. The project mainly aimed at realizing the structural parts with high molding quality through the reasonable design of the atmospheric pressure-driven thermal flow process, to significantly reduce the cost of tooling equipment and the dependence on the traditional super large autoclave molding equipment. At the same time, she also participated in the research on the material selection of the rear pressure frame of the grid structure composite material and the low-cost liquid forming process, to realize easy to pave and fast to lower the cost of the complex surface.
School of Physical Science and Engineering
Professor GE Jianmin from the Institute of Acoustics of the School of Physical Science and Engineering undertook the research project on the optimization design of an acoustic test of a large aircraft cabin structure. The project was to establish the theoretical method and calculation model for predicting the medium frequency (150~500Hz) noise of the engine room structure and predict the noise in the cabin. The noise in this frequency band was the weak link of the aircraft structure, which directly affected the A sound level in the cabin (whether it was up to standard). It is of great theoretical and practical significance to optimize the acoustic design of the engine room structure by establishing the theoretical method and calculation model for predicting the intermediate frequency noise of the engine room structure.
Professor GE's team has undertaken research projects in vibration and noise reduction of large aircraft thin-wall structure assembly, improvement of product quality, sealing, and airworthiness certification, and has supervised doctoral and master's students for COMAC Shanghai Aircraft Design and Research Institute. The project was mainly to cooperate with Shanghai Aircraft Manufacturing Co., Ltd. to complete bolt and rivet tests under various hammer and rivet pressures, identify the corresponding sound and vibration transmission path, and proposed measures to improve the aircraft assembly quality, such as constraint control, local damping control, sound absorption and noise reduction control, and rivet hammer source strength control, which provided technical support and support for the aircraft to meet the noise standards required by airworthiness.
School of Mechanical Engineering
Professor YU Yaobao from the School of Mechanical Engineering participated in the expert group of the large passenger jet joint engineering team. Aiming at the requirements of the large-scale and super large hydraulic system of the aircraft, he established a multidisciplinary integrated temperature analysis simulation platform and an active oil temperature control method for the hydraulic system of the large passenger aircraft under flight conditions, which were applied to the quantitative analysis and qualitative prediction of the overall design and selection of C919 passenger jet. The team put forward the performance reconstruction theory of high-end components in a wide temperature range, revealed the mechanism of electro-hydraulic servo valve blockage, drift, sticking, and "leakage,” solved the technical problem of high-end electro-hydraulic servo valve zero drift suppression in extreme environments. The results were applied to the aero-engine digital control system.
LI Jing, an associate professor of the same school, participated in the joint engineering team of the C919 large passenger jet scheme demonstration. He served as a member of the expert group on the hydraulic energy system, headed the research project on temperature control of the hydraulic system of large passenger aircraft, built a dynamic temperature simulation calculation platform for the hydraulic system of large passenger aircraft, and realized the dynamic temperature calculation of all key nodes of the hydraulic system of large passenger aircraft in full flight profile and under various complex working conditions. He also participated in the research project of aircraft level virtual integrated test system and completed the development and integration of a hydraulic system temperature parameter model. Meanwhile, he participated in the research of civil aircraft system integration design and airworthiness verification technology and completed the simulation modeling and analysis of hydraulic system integration design. The research results provide technical support for the performance optimization design of the hydraulic system of the C919 large passenger jet.
In addition, Tongji teams also participated in establishing a large aircraft intellectual property management system, patent early warning analysis, trade secret management mode, and other consulting services.